Our experiment will be contained in a aluminium
box properly insulated with foam panels. The housing has to withstand
thermal and mechanical loads during the various mission phases. The box structure is basically a sandwich built
with foam core and aluminium skins. The external aluminium case provides
a first thermal and mechanical protection as well as an interface for
experiment mounting on the payload gondola. The internal aluminium case
provides support for internal components: battery pack and an electronic
board.


Aluminium
boxes are built with panels connected with “L-shaped” corners and rivets.
Foam panels are placed in between and glued to the metal cases.

Detailed CAD drawings of the experiment box and
attachment system are shown in the following figures. Please note that
the dimensions reported in drawings slightly differ from actual total
size of the box because they do not include corners and rivets
thickness.
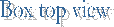
_2_small.gif)

+foam_2_small.gif)
The box is provided with
brackets on the 4 sides. All of them are required to attach the
experiment to calibration devices, mainly tilt and rate table.
Connection to the payload gondola is assured by two beams placed under
the experiment box.


Two sets of mounting bar have been developed to
match the gondola rails in both side of the gondola, the larger and the
narrower (320 – 375 mm).

Considering the thickness of
rivets and “L-shaped” corners, the overall experiment dimension is
21x21x17 cm. The final mass is 3300 g.
More details about experiment
mass budget in the section "Mass & Power
Budget".

FEM structural analysis
demonstrates that the experiment box can withstand to all loadings that
it will encounter during the flight. The worst case mechanical load is
encountered when the parachute opens, and the experiment will be loaded
with 10 g along the Z-axis. The situation has been simulated using FEM
software. The model is a box made of sandwich panels where the core has
no bending stiffness; The constrains are no rotation and no translation
for all the nodes in the bottom panel. The results are shown below:

The maximum total translation
is 0.1 µm for the nodes that are in the centre of the top panel.
Stresses also are low, not exceeding 36 kPa, well below the yield stress
of the aluminium.

Loads due to
thermal gradient has been evaluated, particularly stresses generated on
constrains (where the box is connected with the payload gondola) by
shrinks of the experiment box as the temperature decrease considerably.
However, the values are so low that are not a reason of concern.
|