L'idea di montare un musone
a prua del mio M100 nasce dalla dispiacere nel sentire la cima dell'ancora
strusciare sul tubolare ad ogni salpata d'ancora.
Ho provato a risolvere la cosa mettendo
un parabordo di traverso sulla prua, inutilmente.
Per evitare il contatto cima/tubolare
l'unico modo è sporgersi dal tubolare ma, salpare 6 kg d'ancora
e 6 metri di catena da 8 in quella posizione, è parecchio faticoso.
Unica soluzione è un musone con
la sua bella carrucola scorrisagola che tenga la cima lontana dal
salsicciotto.
Ho iniziato a fare qualche ricerca ma
non ho trovato nessuno che vendesse un musone già pronto adatto
all'M100 quindi ho pensato di arrangiarmi costruendone uno a mio
gusto e piacimento.
Requisiti indispensabili:
1 - un posto dove poter lavorare
facendo rumore, puzza e polvere senza ricevere una citazione dai
vicini o condomini;
2 - un po' di manualità e dimestichezza
con il bricolage, qui da noi si dice che "non bisogna avere due
mani sinistre ".
Bisogna saper lavorare di seghetto,
taglierino e carta vetrata per costruire la sagoma del musone, saper
laminare la vetroresina, stuccarla, lisciarla e verniciarla per
completare il lavoro. Se non si sono mai fatti questi lavori, secondo
me per nulla difficili, bisogna avere un po' di coraggio e provare,
al massimo si butterà via qualche decina di euro di materiale;
3 - avere un po' di attrezzatura,
necessaria soprattutto per la verniciatura, oppure un amico carrozziere.
Dato che dovevo costruirne un solo pezzo
ho scelto di non costruire lo stampo esterno ma una sagoma di polistirolo
( facilmente lavorabile ) da rivestire all'esterno con la vtr. Lo
stampo garantisce sicuramente che la superficie esterna del pezzo
sia perfettamente liscia ma è lungo e difficoltoso da costruire
per una sagoma così complicata.
Invece laminando sopra la forma la superficie
sarà sicuramente irregolare e dovrà essere stuccata e lisciata ma,
secondo me, il maggior tempo speso per rifinire il pezzo è sicuramente
meno di quanto necessario per fare lo stampo.
Preparazione della
sagoma
Materiale necessario:
- sagoma di polistirolo,
- seghetto,
- taglierino,
- carta vetro,
- silicone.
Ho preso un po' di misure sul gommone
e poi sono andato in una ditta che lavora il polistirolo per farmi
tagliare le sagome base, un semicilindro del diametro del tubolare
e la sagoma di massima del musone.
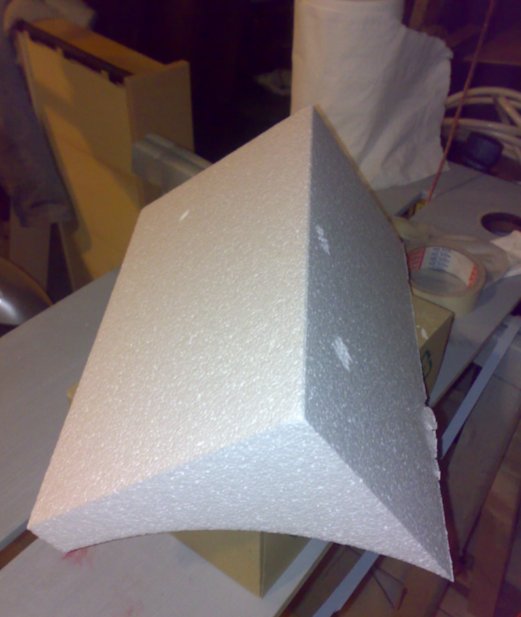
Poi le ho unite con un po' di silicone
per vedere che effetto faceva e per iniziare a dargli la forma.
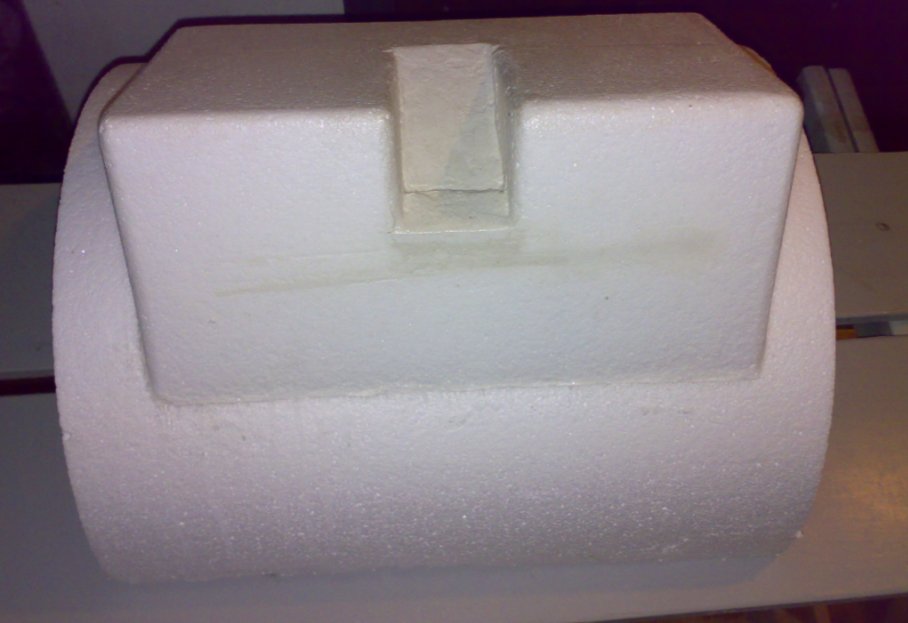
.Con il tagliabalsa
ho ricavato la sede dello scorrisagola e ho iniziato ad arrotondare
gli spigoli con la carta vetrata.
Per una buona riuscita
è meglio scegliere polistirolo di alta densità altrimenti le palline
di cui è composto quello leggero iniziano a volare ovunque e non
si riesce ad ottenere una superficie regolare.
I fianchi della forma
non devono essere perfettamente verticali ma devono essere inclinati
verso l'interno nella parte alta per facilitare l'estrazione a fine
lavoro della forma di vtr.
Ho riempito gli angoli
vivi con del silicone e li ho arrotondati passando con la punta
di un dito bagnata in acqua saponata prima che il silicone si indurisse.
E' importante lasciare
un bordo di almeno 5 cm tutto intorno al musetto, sarà la base di
appoggio sul tubolare.
Rivestimento
di vetroresina.
Materiale necessario:
- Cera distaccante,
- Resina bicomponente
liquida per laminazione, meglio se la epossidica , inodore, ma più
costosa e più difficile da trovare in commercio. Altrimenti quella
poliestere, puzzolente, meno costosa, facilmente reperibile, ma
bisogna fare attenzione perché corrode il polistirolo.
- Tessuto di vetro
almeno da 250 gr/mq, meglio se con trama in diagonale perché segue
meglio le curve, pennelli a setole rigide, diluente nitro per pulizia.
- Una bilancina precisa
per dosare resina e catalizzatore.
Prima di applicare la
vetroresina bisogna cospargere la forma con un paio di mani abbondanti
di distaccante, si trova in colorificio. Per un buon risultato bisogna
avere una temperatura di almeno 20° poco umida ed il tempo necessario
a terminare la ricopertura senza interruzioni. Nelle
stagioni più calde è meglio evitare di lavorare al sole perché la
resina indurisce troppo velocemente e potrebbero formarsi delle
bolle.
Ho tagliato innanzi
tutto le pezze di tessuto necessarie tenendole abbondanti di circa
5 cm per lato, prevedendo 3 strati .
Dopo aver miscelato
resina e catalizzatore nelle proporzioni consigliate ho steso una
mano di resina su una faccia della forma ( meglio iniziare dal lato
superiore, dove si camminerà ) poi ho appoggiato la pezza di tessuto
"picchiettandola" con la punta del pennello sempre bagnato di resina
finchè diventa trasparente, segno che è ben impregnata. Non bisogna
dare pennellate alla lunga come per verniciare perché il tessuto
si sposta.
Negli angoli il tessuto
fà sempre le bizze e non vuole stare attaccato, basta tagliare con
una forbice in diagonale e tutto si sistema. Ho seguito lo stesso
procedimento per i fianchi e la base.
Terminato il primo strato
ho steso subito i successivi prima che lo strato precedente fosse
asciutto, in questo modo si ottiene un corpo unico ed il massimo
della robustezza. Alla fine della laminazione il risultato era questo.
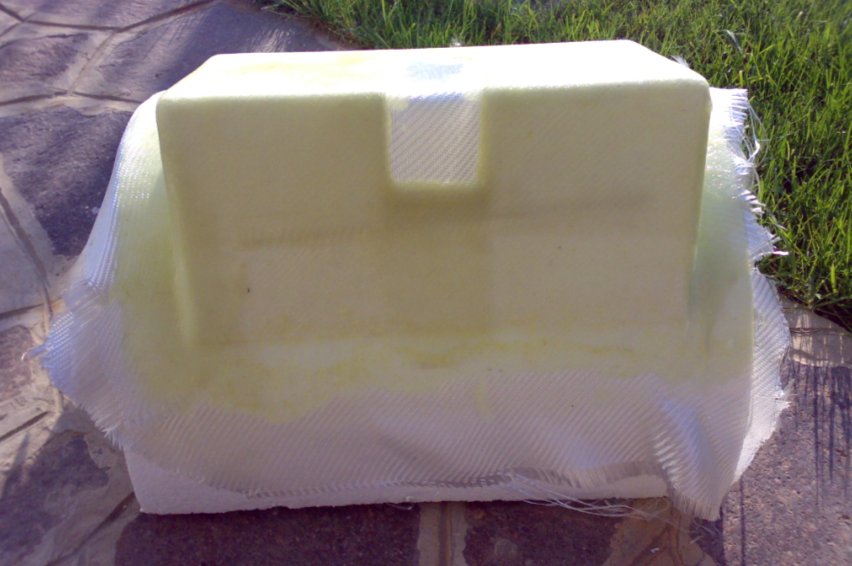
Trascorse 24 ore sarà possibile togliere
il pezzo lavorato dalla forma di polistirolo, sperando che il distaccante
abbia fatto il suo lavoro. Se abbiamo dato le giuste inclinazioni
alle facce verticali il pezzo si staccherà facilmente.
Se troveremo difficoltà piuttosto che
fare forza sulla forma che, in questa fase è ancora leggera e non
sufficientemente robusta, è meglio "fare a pezzi" il polistirolo
dall'interno.
Separate le due parti mi sono ritrovato
con un abbozzo di musone tra le mani, la prima cosa da fare è tagliare
grossolanamente le parti di tessuto in eccesso.
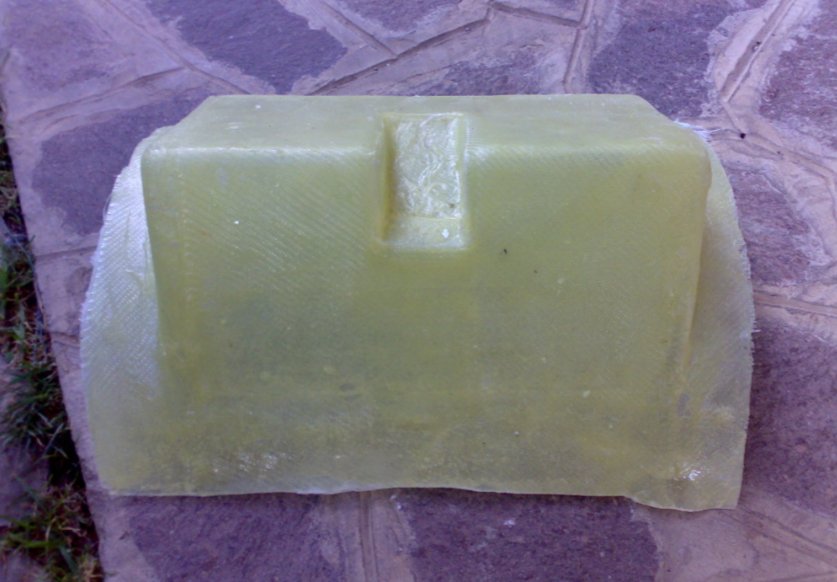
Successivamente ho pulito l'interno
da qualsiasi traccia di polistirolo e distaccante, usando diluente
nitro ed acetone.
Ho iniziato quindi a rinforzare dall'interno
il musone facendo attenzione a mantenere le zone che andranno a
contato del tubolare il più possibile lisce e regolari.
Per fissare saldamente lo scorrisagola
e la galloccia ho preparato una tavoletta di compensato marino spessa
12 mm e l'ho incollata usando sempre la resina epossidica bicomponente.
Poi ho rivestito con altri 3 strati
di tessuto e resina tutto l'interno, tavoletta compresa, seguendo
lo stesso procedimento della parte esterna ottenendo uno spessore
di circa 4 mm nelle pareti e circa il doppio negli angoli per via
dei sormonti del tessuto, più che sufficienti a garantire la robustezza
necessaria.
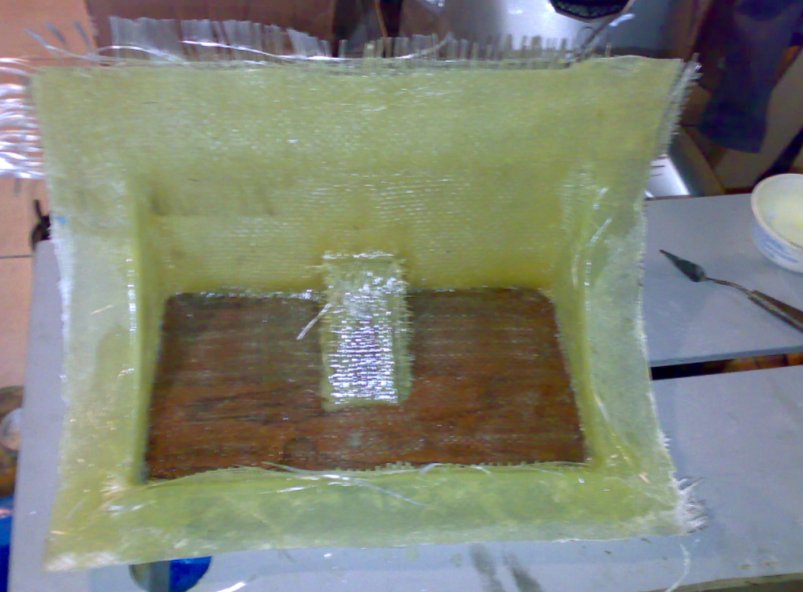
Per rendere antisdrucciolo la parte
calpestabile per la salita a bordo ho incollato un pezzo di un coperchio
di un gavone recuperato tra gli scarti di un cantiere nautico, usando
la stessa resina della laminazione e mettendo tutto sotto pressione
con dei morsetti.
Trascorse almeno 24 ore si può iniziare
la fase più barbosa, la rifinitura....
Fine prima parte - Segue
by MaxM100
Last
Update 13.06.07
|