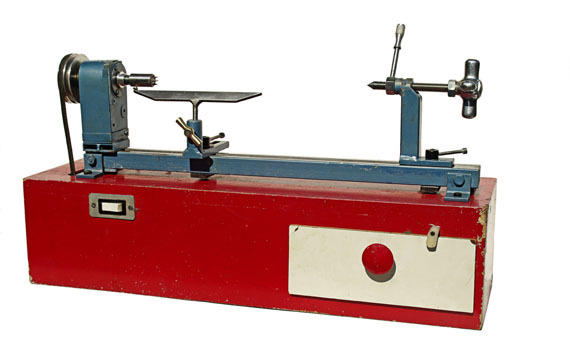
|
Distanza tra le punte = 300 mm. - Diametro massimo tornibile 100 mm.
|
Il tornio da legno si presta molto bene all'autocostruzione perché, diversamente da quello per metallo, non richiede un'elevatissima precisione di lavorazione delle parti. Lo si può quindi realizzare con un'attrezzatura di base e con materiali di recupero o di facile reperibilità: morsa, sega da ferro, lime e un trapano con supporto a colonna; la saldatrice è utile, ma se non la si possiede si può anche montare il tutto con viti, ribattini e un po' d'ingegno.
Naturalmente sto parlando di macchine di ridotte dimensioni e potenza, quindi più da modellista che da falegname, ma nulla vieta di passare a misure più grandi, adeguando la robustezza delle parti e preparandosi ad un lavoro molto più impegnativo; credo però che pochi hobbisti intendano realizzare gambe per tavoli.
Con pezzi prevalentemente di recupero ne ho già costruiti tre, due per gli amici ed uno per me; questo, essendo il primo prototipo, è anche il più brutto e non fa che confermare il detto che "il calzolaio ha le scarpe rotte". Ho sempre qualche altra realizzazione che prende la precedenza e poi mi ha dato tante soddisfazioni facendo bene il suo lavoro, quindi mi ci sono affezionato.
Per d'are un'idea delle dimensioni, la distanza tra le punte è di 300mm. e il diametro massimo tornibile è 150mm.
|

|
Ecco una versione migliorata, con motore più potente e cono pulegge che consente la scelta tra tre velocità: |
|
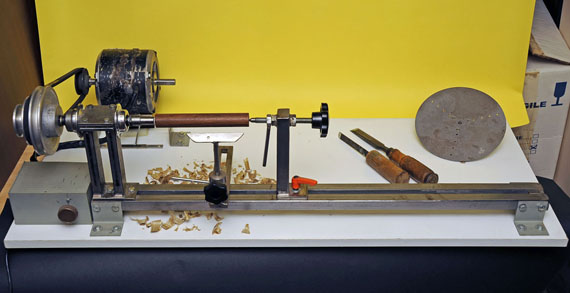
|
|
|
|
LA STRUTTURA
|
Il bancale che sostiene il tutto e forma le guide di scorrimento per la contropunta e il poggiaferro è fatto con due segmenti di profilato rettangolare; alle estremità sono inseriti come distanziali due spezzoni dello stesso profilato con l'aggiunta di una fettina di latta ricavata da un barattolo, così si crea il gioco necessario a consentire lo scorrimento della contropunta e del poggiaferro, che sono impostati su due pezzi dello stesso profilato. Due bulloni passanti assemblano il tutto insieme a quattro squadrette, ricavate da un pezzo di angolare, che saranno i piedi di fissaggio.
|
|
|
|
LA TESTA
|
Detto in parole terribilmente povere, occorre un perno che giri per mettere in rotazione il legno.
L'approccio più semplice si ha usando la trazione diretta, cioè sfruttando direttamente l'albero di un motore elettrico. Questo sistema presenta due limiti importanti: non è facile ottenere la giusta velocità di rotazione poiché molti motori girano troppo velocemente e il corpo del motore ha un ingombro che ostacola il lavoro su pezzi di piccolo diametro.
IL MOTORE
I motori da preferire,per la silenziosità, la velocità costante e la possibilità di lavorare a lungo senza surriscaldarsi, sono quelli a induzione.
Esistono anche motori ad induzione a tre velocità, per esempio quelli dei ventilatori e quelli dei termoconvettori; la resa è buona a tutte le velocità perché è ottenuta con commutazione degli avvolgimenti appositamente predisposti.
I motori a spazzole hanno generalmente diametri più contenuti, ma ruotano velocità molto alte e non costanti. La velocità può però essere variata in un ambito molto ampio collegandoli ad un regolatore elettronico; ci sono due categorie di regolatori: i "dimmer" che si usano anche come attenuatori per le luci e i variatori specifici per trapano. Con i primi la potenza del motore si riduce di molto a bassi regimi di rotazione; con quelli per trapano si mantiene una buona coppia anche a velocità minime, ma il motore ha un funzionamento discontinuo a vuoto, cioè quando non è sotto sforzo.
Va considerato anche che riducendo i giri diminuisce parallelamente il flusso d'aria della ventola di raffreddamento e il motore tende a scaldarsi parecchio; a questo si unisce il fatto che i motori a spazzole sono molto più rumorosi e soggetti a maggior usura nell'uso prolungato.
|
|
|
Motore da termoconvettore(a induzione)
|
Motore da aspirapolvere(a spazzole)
|
|
|
Altro motore da termoconvettore con albero molto lungo
|
Motori da ventilatore(a spazzole)
|
L'ALBERO
L'altra soluzione, che poi è la migliore, prevede l'impiego di un albero su cuscinetti, munito di pulegge per accoppiarlo al motore, che quindi può essere piazzato dietro o sotto al tornio. In questa maniera si possono montare dellle pulegge a gradini e cambiare la velocità spostando la cinghia. Le pulegge a gradini sono componenti costosi e non certamente facili da reperire come pezzi di recupero, specie quelle di piccole dimensioni, quindi suggerisco due soluzioni più economiche: montarne una sola sull'albero del tornio, mentre sul motore si monta solo una puleggia piccola; il motore va poi sospeso "a cerniera" su di un perno in modo che possa scorrere avanti e indietro per allineare la cinghia alla gola scelta di volta in volta, mantenendo la tensione per gravità. Si può anche ripiegare inizialmente su una puleggia a singola gola, quindi su una sola velocità e poi, a tornio funzionante, realizzare le pulegge tornendole da un blocco di legno duro e compatto. L'albero della testata è soggetto anche ad una spinta assiale, quindi a rigore dovrebbe essere dotato di cuscinetto conico o reggispinta; la spinta è però modesta e per piccoli torni come il mio non ho mai riscontrato problemi con l'uso dei normali cuscinetti a sfere. Esistono anche dei cuscinetti a gola profonda, che sopportano bene moderate spinte assiali.
L'albero non si può costruire se non si dispone di un tornio per metalli, ma è molto facile reperire qualcosa di adatto, o adattabile, tra i rottami; al massimo si potranno sostituire, con poca spesa, eventuali cuscinetti usurati. Per esempio un albero molto robusto, ma ingombrante, è quello che sostiene il cestello delle lavatrici, mentre elementi di piccole dimensioni si possono trovare smontando una vecchia fotocopiatrice.
|
LA CONTROPUNTA
Anche questa parte è semplificata al massimo, quindi niente contropunta rotante, che oltretutto avrebbe un ingombro incompatibile con le torniture da modellismo. Semplicemente un pezzo di barra filettata M10 con un'estremità resa conica montandola nel mandrino del trapano e facendola ruotare contro la mola; in questo modo si ottiene un cono ben centrato.
Nell'uso, basterà un minuscolo pezzetto di cera nel foro per consentire al legno di ruotare sulla contropunta con pochissimo attrito.
La barra filettata si avvita in un pezzo cilindrico forato e filettato che viene fissato sopra una colonnina di profilato chiusa in basso da una piastrina, con lo stesso sistema di fissaggio della testata. Qui però bisogna portare il bullone all'esterno della colonnina e fissarlo con un dado munito di manettino che permette di sbloccare la contropunta e farla scorrere sulle guide. Le foto comunque chiariscono bene come va costruita. Nelle foto si vede anche che il tenone della contropunta l'ho sostituito con un quadrello massiccio, ma non è indispensabile farlo.
Un altro dado con manettino (io ho usato un bulloncino a brugola) serve a bloccare la barra filettata dopo ogni regolazione.
|
|
|
IL POGGIAFERRI
E' il supporto regolabile che serve a sostenere lo scalpello durante la tornitura: ne ho fatti due di diversa lunghezza.
Il supporto presenta un'asola per lo spostamento diametrale che ho costruito saldando 4 pezzi di barretta, ma che si può realizzare praticando una serie di fori in una piastrina e poi rifinendo di lima. Amche qui, se non si dispone della saldatrice, è possibile farne a meno se si fissa con due viti il supporto cilindrico alla piastrina.
|
|
|
Quando si è montato il tutto, è oppurtuno registrare i dadi di bloccaggio in modo che l'arco di movimento dei manettini si collochi nella parte posteriore del tornio, così non intralciano durante la tornitura. Basta procedere per tentativi inserendo rondelle di vari spessori.
|
LA PUNTA DI TRASCINAMENTO
Il perno dei mozzi da bicicletta è filettato con un passo inusuale, quindi è necessario conservare i dadi originali. Nella prima versione ho preso uno di questi dadi e ci ho praticato un intaglio trasversale in cui ho fissato una piastrina, dalla quale ho ricavato con la lima le tre punte che infisse nel legno ne permettono il trascinamento. Nella versione successiva sono partito da un pezzo cilindrico forato per inserirlo sull'albero, dove viene fissato con una vite. In testa ho praticato quattro piccoli fori, uno centrale e tre attorno, inserendoci dei chiodi di acciaio appuntiti, bloccati semplicemente con qualche colpo di bulino, tanto lavorano sempre a spinta. La punta centrale è leggermente più lunga delle altre. Con questo "mandrino" mi riesce molto più agevole la centratura del legno.
|
|
IL PLATORELLO
|
Si tratta di un elemento indispensabile per la tornitura a sbalzo di pezzi con lunghezza ridotta. E' sostanzialmente un disco metallico che va fissato sull'albero al posto della punta di trascinamento. sul disco sono praticate tre (o quattro) feritoie radiali per il passaggio delle viti di bloccaggio del pezzo di legno. Purtroppo la sua realizzazione richiede un tornio da metalli, ma con qualche astuzia si potrebbe anche farne a meno; naturalmente non verrà perfetto, ma servirà allo scopo. Vediamo come.
Il disco che ho usato, l'ho ritagliato col seghetto alternativo da un pannello d'alluminio di 3mm. e l'ho rifinito sul tornio, ma si può usare un disco di ferro che si trova, già tagliato, dai rivenditori di materiali ferrosi. Le fenditure si ricavano praticando, dopo un'accurata tracciatura, una serie di fori e rifinendo di lima. La bussola è il pezzo più difficile ma si può trovare qualche pezzo adattabile smontando dei vecchi rubinetti; sarà probabilmente necessario inserire uno o più spezzoni di tubo per adattare il diametro del foro al perno. Il fissaggio della bussola al disco si ottiene con tre viti, curando bene la centratura.
|
|