Supponiamo di dover
ricostruire da zero paramezzale e pagliolato di un gommone
smontabile... Sapreste come procedere?
Mettendo insieme i suggerimenti
di Pogo e Nicasta, si può fare...
Ovviamente questo è un
caso estremo, ma partendo da qui si potrà facilmente
adattare il procedimento alle proprie necessità, utilizzando
solo le informazioni che servono...
|
Innanzitutto mandiamo a mente
alcune nozioni "base" che ci torneranno molto utili
nel nostro lavoro:
1) generalmente il pagliolato
di un gommone è formato da 5 o più elementi,
di cui i primi tre da poppa hanno forma rettangolare e sono
tutti uguali, in larghezza e in lunghezza, per motivi sia
di economia di produzione che di stivabilità. In funzione
delle dimensioni del gommone e del diametro dei tubolari,
la larghezza varia tra i 90 ed i 100 cm, mentre la lunghezza
è compresa tra i 50 ed i 60 cm. Completano il piano
la tavola di mastra, a prua estrema, che spesso è incollata
alla gomma, ed il pagliolo immediatamente successivo, che
hanno forma trapezoidale.
Il profilo dei lati obliqui potrebbe
essere rettilineo (caso dei gommoni con tubolari a ferzi radiali,
tipo Zodiac , Callegari, Bat etc) oppure arcuato (gommoni
con tubolari a taglio longitudinale, più filanti)...
qui va valutato in base, se possibile, a foto di un gommone
simile...oppure determinato per tentativi.
|
 |
 |
2) la larghezza del paiolo è l'unica
misura certa rilevabile quando si dispone della sola parte
in gomma.
Basta misurare la distanza INTERNA
tra i tubi nel punto in cui il foglio del paiolato fa contatto
con lo specchio di poppa ... il settore di poppa DEVE necessariamente
raccordarsi allo specchio, per cui la sua larghezza coinciderà
con la distanza misurata sullo specchio in corrispondenza
dell'attaccatura tra tubolari e fondo (il doppio di quella
evidenziata nella figura).
Se c'è, potete usare il
profilo di guida sullo specchio come riferimento dell'altezza
a cui prendere la misura.
In questo modo avrete in un colpo
solo la misura di tre paglioli.
|
3) Anche la tavola trapezia ha
di solito la stessa lunghezza di quelle rettangolari.
La tavola di mastra,( in azzurro
nella foto) ha invece dimensioni proprie, ed di solito è
più piccola. Per fortuna,però, su molti gommoni
è incollata al tubolare a prua, per cui è molto
difficile a perdersi. Supposto che ci sia, potrete usarla
per trovare con buona approssimazione anche la forma della
seconda tavola (la sua larghezza varia, ovviamente, tra quella
dei settori rettangolari (base maggiore del trapezio) e quella
della tavola di mastra (base minore), che deve raccordare
tra loro)
|
 |
 |
Anche la lunghezza di ciascuna
singola tavola resterà determinata semplicemente dividendo
per quattro la distanza tra lo specchio di poppa e l'estremo
della tavola di mastra misurata a gommone GONFIO.
Se la lunghezza risultante di
ciascun settore supera i 60-65 cm di lunghezza, meglio dividere
in cinque, altrimenti i pannelli diventano troppo ingombranti
Se siamo stati fortunati, la prima
parte del lavoro è fatta.
Se invece la tavola di mastra
manca, la cosa si fa leggermente più complessa perchè
bisognerà trovarne la sagoma per tentativi usando dime
di cartone o legno "a perdere".
I pannelli del pagliolato andranno
realizzati in multistrato marino Okoumé da 1 cm. o 1,2 c.
di spessore.
il problema del multistrato non
marino ( pioppo , betulla , faggio , ecc. ecc. ) non è tanto
il legno che tende ad impregnarsi d'acqua , bensì la
qualità della colla che tiene i fogli uniti ... infatti
nel multistrato marino (okume', mogano) i fogli che compongono
il multistrato sono incollati con colle resorciniche non solubili
in acqua , mentre in quelli non marini sono incollati con
colle viniliche che sono idrosolubili ... quindi il rischio
è che una volta bagnato il multistrato si gonfi e si sfogli
come una fetta di torta millefoglie ...
|
Il punto più critico in assoluto
è la linea di appoggio dei pannelli sui tubolari, in
cui il legno tocca (e stira ) le giunture dei tubolari....non
deve assolutamente esserci nessuna asperità o spigolo
che possa, per effetto del movimento abradere il tessuto.
Il legno deve essere più liscio
possibile senza appigli.... In genere ci possono essere due
soluzioni:
o smussare e dolcemente raccordare
il pannello,
oppure aggiungerci una cornice
longitudinale cilindrica che ripartisca lo sforzo (tipo manico
di scopa scanalato, per intenderci...).
|
|
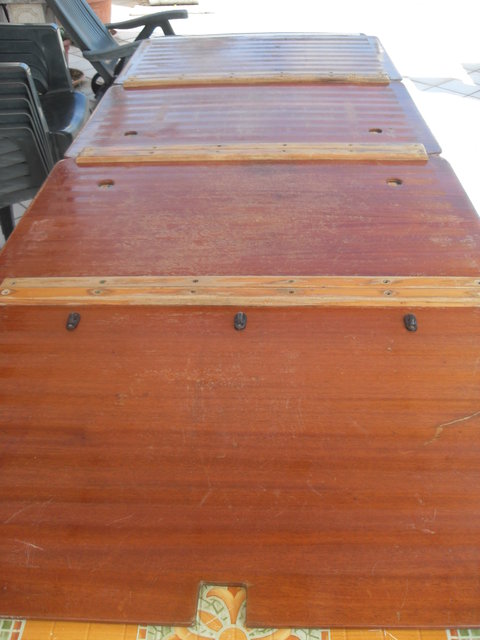 |
Il pagliolato andrà poi
completato con i "bagli", ovvero dei listelli
trasversali di irrigidimento ed eventualmente i "longheroni".
Insieme costituiranno un telaio per cui sono ottimi listelli
in mogano sezione 2 x 3 cm,. facilmente reperibili nei Bricocenter.
Mentre i bagli sono pressochè
obbligatori per ottenere una sufficiente resistenza, i longheroni
spesso non sono presenti, e per tenere in squadra il pagliolato
ci si affida all'azione di compressione dei tubolari.
Questo avviene soprattutto laddove
il paramezzale abbia uno spessore molto consistente, come
per esempio nell'Alcione Callegari.
Qui il pagliolato è semplicissimo:
Pannelli piani e bagli , opportunamernte accorciati e smussati
alle estremità per evitare nel modo più assoluto
che possano toccare i tubi.
|
Ora che abbiamo il pagliolato
definitivo, passiamo a determinare, almeno approssimativamente,
la forma del paramezzale.
Per la parte di poppa possiamo
già montare i primi due elementi di pagliolato definitivi...
a prua invece per lavorare
comodi, converrà realizzare una dima a "scaletta"
per tenere in forma correttamente il i tubolari che "simuli"
la presenza del pagliolato ma senza ostacolare la possibilità
di accedere alla parte sottostante per prendere le misure
di altezza del nostro paramezzale.
Più misure prenderemo,
più precisa sarà la nostra opera.
Per far ciò, si usano due
longheroni (vanno bene due manici di scopa) , tenuti distanziati
da una serie di traversi, a simulare la presenza dei paglioli,
|
Anche per realizzare il paramezzale
potremo sfruttare come base di partenza alcune regole base:
1) L'altezza del paramezzale a
poppa resta determinata dalla distanza tra la sommità
del "tacco" di appoggio sullo specchio e la cuspide
della "v" dello specchio ( in rosso nela foto a
destra..
2) Allo stesso modo la larghezza
interna del tacco ci darà lo spessore del paramezzale.
3) il profilo della parte inferiore
del paramezzale nella metà di poppa, è perfettamente
piano, senza insellatura... in caso contrario otterremo non
un gommone ma una gondola, Analogamente la superficie superiore
del paramezzale dovrà essere ancora piana, stavolta
per appoggiarvi stabilmente i paglioli.
4) l'altezza ideale del paramezzale
è quella che in <ogni punto tiene perfettamente
teso il telo di carena senza però sottoporlo a tensioni
" da corda di violino"
5) se costruite un paramezzale
in misura abbondante, si rischia che la maggiore tensione
sul telo laceri il telo stesso o lo scolli dai tubi ... ricordatevi
che molto probabilmente stiamo parlando di un gommo con parecchi
anni sulle spalle, che non è il caso di stressare oltre
il dovuto ...
|
|
Tenendo presenti queste semplici
regolette iniziamo i nostri rilevamenti da poppa.
Montiamo i primi due settori del
pagliolato, lasciando in mezzo una fessura di circa 2 cm e
gonfiamo il gommo.
Posizionare il gommone su due
appoggi laterali sotto i tubolari in modo da lasciare libero
di estendersi verso il basso il telo di carena.
Mettiamo a contatto con il fondo
del gommo un listello piano largo come la cava sul tacco e
lungo circa 1,5 m, che simulerà il nostro "dritto
di chiglia".
Ora inseriamo un "puntone"
nella fessura tra i due paglioli, spingiamo sul listello di
fondo e misuriamo quanta profondità serve per mettere
in tiro il telo di fondo.
Per verifica, possiamo ripetere
la misura inserendo il terzo settore del pagliolo e misurando
la profondità tra secondo e terzo pagliolo.
|
Congiungendo i tre punti (altezza
al tacco di poppa e misure rilevate),,
otterremo il profilo della semitrave di poppa, sino al ginocchio
di snodo.
Le misure di altezza così
rilevate dovranno essere aumentate di 20 mm nel paramezzale
definitivo, in modo da tendere meglio il tutto.
Il profilo dovrebbe risultare
come quello in basso in figura, con due linee piane leggermente
divergenti e il lato verticale verso lo specchio di poppa
opportunamente inclinato per appoggiare su tutta l'altezza.
Ripetiamo ora il procedimento
per la metà di prua, usando la dima a scaletta invece
del pagliolato, in modo da avere più puntoi di misurazione,
data la forma più complessa della ruota di prua.
Il ginocchio è la parte
più complicata da spiegare... in pratica si deve realizzare
il profilo di un semicerchio maschio/femmina in modo che le
due metà possano ruotare una sull'altra spingendosi
mutuamente... conviene copiarla pari pari da un altro gommone.
Anche per il paramezzale il legno
ideale è il multistrato marino.
La conifera è inadatta, sia abete
che laric, per via delle fibre poco compatte. In ogni caso,
anche con legni migliori, è sconsigliabile realizzare il paramezzale
in massello. Le fibre incrociate di un multistrato garantiscono
maggiore rigidità strutturale.
Anche i fori passanti per i bulloni
di serraggio del ginocchio sarebbero un pericoloso punto di
innesco di rottura.
I bulloni per il fissaggio devono
passare per l'asse del paramezzale per formare il movimento
a ginocchio ...
|
|
 |
Passiamo ora alla verniciatura.
Dopo la realizzazione, i pannelli
dovranno essere ulteriormente protetti e lo si potrà fare
in diversi modi: 1) Impregnante + Flatting oppure 2) Impregnante
+ Fondo turapori + Vernice poliuretanica bicomponente; oppure
3) Resina epossidica bicomponente + Vernice poliuretanica
bicomponente, I tre metodi sono indicati in ordine di "resistenza"
agli agenti marini (e risultano anche in ordine di "costo).
Il flatting è la finitura marina
per antonomasia, utilizzata in tutto il mondo da decenni.
ha un buon potere protettivo, ma con l'inconveniente che,
non avendo protezione anti UV sotto il sole "cuoce" e dopo
un po' ingiallisce e si spellicola. Il pezzo necessita quindi
di una manutenzione frequente.
La poliuretanica bicomponente,
più recente rispetto al flatting, è molto più resistente all'azione
degli agenti atmosferici e stesa sul pezzo crea uno strato
protettivo "gommoso" che non tende a distaccarsi dal pezzo,
contrariamente al flatting.
|
Io preferisco comunque il Flatting.
Suggerirei di procedere preventivamente
con due mani di impregnatura utilizzando lo stesso flatting,
diluito al 50% col suo diluente, che dovrebbe essere il sintetico.
In questo modo il prodotto penetra meglio nelle fibre del
legno, preservandolo maggiormente dall'umidità e dall'acqua.
Dopo queste due mani di flatting molto diluito, si procede
con 2 mani di finitura sempre con flatting, questa volta puro
o diluito al 10%. Con l'impregnatura preventiva la pellicola
finale si aggrappa anche meglio ed impiega più tempo a sfogliare.
Anche per il paramezzale, volendo
tener d'occhio anche l'aspetto economico, il flatting va bene.
|
|
|