In questa pagina ci sono tutte le modifiche che
abbiamo aggiunto ai nostri Raptor per vedere di migliorarne le prestazioni.

Come prima cosa abbiamo montato il servo del passo di coda piu'
indietro sul telaio, all'altezza del supporto tubo di coda.
Il comando e' stato poi sostituito con un tubo di carbonio diametro 5 mm esterno e 3 mm
interno, terminato da due spezzoni di barra filettata da 3mm incollati con epossidica UHU
plus. Sulla barra filettata sono invitati due uniball con filetto da 3mm e sfera piccola
standard.
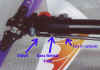
Mio fratello ha mantenuto il comando originale in acciaio opportunamente accorciato e
guidato lungo al tubo dalle guide originali.
Non ci sono differenze di funzionamento fra i due sistemi, la cosa essenziale e' che il
comando sia scorrevole e privo di giochi.

Altra utile modifica e' stata quella di realizzare una piccola
paratia in lamierino (in plastica su quello di mio fratello) per convogliare
l'aria della ventola sulla testa del motore e migliorare il raffreddamento. Senza
questa paratia l'aria lambisce solamente la testa motore e poi si disperde dentro la
fusoliera. E' importante che la paratia sia appoggiata nella sua parte posteriore al
condotto curvo di raffreddamento ricavato nel telaio per evitare accessive fughe d'aria.
La paratia si fissa facilmante con viti autofilettanti.
Le fotoche seguono sono per fortuna piu' chiare delle parole.
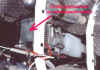

I due tubi di irrigidimento del tubo di coda sono ancorati al telaio a
due piccoli nottolini in plastica ricavati ai lati del serbatoio. Forzando il tubo di coda
lateralmente si vede che questi due attacchi flettono un po'.
Soprattutto se si ha un giroscopio con blocco della coda (heading lock) bisogna ricercare
la massima rigidita' laterale del tubo di coda.
La situazione migliora notevolmente aggiungendo due piccole righette in alluminio (una per
lato) come si vede in foto. Queste due piccole righette, dal peso praticamente
insignificante, scaricano lo sforzo dei tubi di irrigidimento direttamente
sull'attacco del castello motore, ben piu' robusto degli attacchi originali.
Troppe vibrazioni di una frizione mal centrata mi avevano crepato un tubo di supporto. Se
vi capita si possono riparare con l'inserimento di una righettina di alluminio incollata
con UHU plus e poi legata con vetro o carbonio e altra epossidica a fermare il tutto.
Nella foto si puo' notare la mia riparazione, legata con rowing di carbonio.
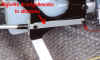

Utilissimo anche se non indispensabile e' la presa esterna per collegar la
candeletta "glow" alla batteria in quanto e' difficilmente
raggiungibile con una normale pipetta. Abbiamo usato una spinetta RCA, quelle che si usano
per le linee negli apparecchi stereo, montata su un semplice supporto in righetta di
alluminio.
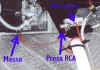

Come gia' accennato da qualche altra parte ho avuto problemi al gruppo
ventola-frizione perche' sul mio elicottero era fuori centro e
trasmetteva vibrazioni ad alta frequenza al telaio. Queste vibrazioni
disturbavano il buon funzionamento del giroscopio, l'ottimo CSM 540.
Il primo segnale di vibrazioni ad alta frequenza e' la presenza di schiuma all'interno del
serbatoio con il modello in volo. Se notate schiuma nel vostro serbatoio fate le indagini
del caso, probabilmente la ventola e' fuori centro, basta qualche decimo di millimetro.
Queste vibrazioni non sono visibili ma sono molto pericolose, oltre ad influire sul
funzionamento del giroscopio possono danneggiare i servocomandi e la ricevente e fare
crepe in particolari metallici, come i tubi che fungono da supporto del trave di coda.
Per vedere se la ventola gira fuori centro c'e' un modo empirico e poco ortodosso; i
puristi si tappino le orecchie. Con il motore in moto al minimo si avvicina poco a poco la
punta di un cacciavite alla parte in alluminio della ventola, si fa con il motore montato
sull'elicottero. Si ferma quindi il motore e si guarda dove il cacciavite ha segnato
l'alluminio, se ha toccato lungo tutta la circonferenza allora la ventola e' centrata.
Il centraggio della ventola non e' comunque un problema solamente del Raptor, al contrario
e' un particolare da curare su ogni elicottero. Solo che la ventola del raptor, come
quella di altri eli classe .30, ha il foro filettato e puo' essere montata in una
sola posizione. Quindi se e' fuori centro rimane fuori centro anche se la smontiamo dal
motore e proviamo a rimontarla di nuovo.
Per rimediare il tutto e' necessario avere a disposizione un piccolo tornio e un perno
filettato ben dritto necessario per montare la ventola sul mandrino del tornio.
Se ne avete la capacita' potete costruirvi un apposito perno con filettatura 1/4 di
pollice con 28 filetti per pollice.
Io mi sono arrangiato cannibalizzando un vecchio albero motore da macchinine di un
Novarossi 3,5 cc.
I motori 3,5 cc da macchinine hanno lo stesso filetto 1/4" 28 TPI dei motori classe
.30 da elicotero e se avete un amico "macchinaro" vi potra' sicuramente fornire
un albero motore in disuso da modificare allo scopo come quello visibile nelle foto che
seguono.
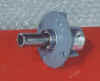
Con uno smerigliatore angolare (in arte detto flessibile) e disco da taglio e' facile e
rapido tagliare l'albero all'altezza del cuscinetto posteriore come si vede in foto. E'
bene tagliare un po' anche della parte anteriore dell'albero per potere lavorare la parte
in alluminio della ventola anche all'interno. Lasciate un po' della parte liscia
anteriore, vi sara' utile per controllare con un comparatore se l'albero e' montato dritto
sul tornio.
Il cuscinetto che si vede nelle foto ha solamente la funzione di spessore, ho usato un
cuscinetto malandato perche' ha le facce sicuramente ben parallele. In alternativa vi
potete comunque costruire uno spessore adatto al tornio.
Vediamo ora le operazioni da seguire per ottenere un bel lavoro:
1) Montare l'albero sul mandrino del tornio e controllare con un comparatore che sia
ben centrato.
2) Avvitare la ventola sul perno con il suo adatto spessore (io ho usato un cuscinetto).
3) Con il comparatore controllare il fuori centro della parte in alluminio della ventola.
Se e' gia' centrata e' inutile intervenire, il problema va ricercato altrove (albero del
vostro motore storto??).
4) Tornire la parte in alluminio interna ed esterna della ventola. Togliere il minimo di
materiale per riportare in centro il tutto. Gia' che ci siete tornite un po' anche il
disco in plastica della ventola, giusto quel po' che serve e non di piu'. E' bene tornire
la plastica solo sul perimetro esterno senza toccare la faccia rivolta verso al motore.
5) Ora bisogna montare la ventola sul motore compreso il controdado.
6) E' arrivato il momento di rimontare la frizione sulla ventola e questa e' un'operazione
delicata in quanto se e' un minimo fuori centro genera anch'essa vibrazioni.
Per fare cio' con la massima precisione ho praticato quattro fori da 2,5 mm poi filettati
3 M in cima al mozzo portafrizione della ventola. I fori sono disposti a 90 gradi uno
rispetto all'altro come si vede nel disegno qui allegato. (Cliccare sull'immagine per
vederla ingrandita)
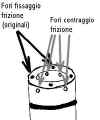
In questi quattro fori vanno invitati quattro grani 3 M che servono per centrare la
frizione sulla ventola, invitando un grano e svitando quello che sta di fronte.
Praticati i 4 fori e filettati gli stessi si procede come segue:
1) Montare la ventola sul motore con anche il controdado. Fissare il motore magari
prendendolo in morsa per una flangia. Fate tanta attenzione a non rovinare il carter.
2) Montare la frizione con le due viti originali un po' lente in modo che possa muoversi
un po'
3) Meglio prima togliere la candelina, poi, facendo girare la ventola rispetto al motore,
controllare con il comparatore il fuori centro della frizione e regolare i quattro grani
in maniera che la frizione sia centrata.
4) Serrare le due viti della frizione per bloccarla in posizione.
E' bene aggiungere un po' di frenafiletti ai quattro grani e poi lasciarli in loco in
maniera che garantiscano un perfetto centraggio della frizione.
5) Ricontrollare il fuori centro una volta che avete serrato il tutto, qualche centesimo
di millimetro e' tollerabile, daltronde la perfezione non e' di questo pianeta!
Una frizione giu' di centro di uno o peggio due decimi di millimetro e' da considerarsi
gia' troppo fuori centro. Almeno per i miei gusti.
6) Rimontare il motore sul modello.
7) Andare a volare il piu' possibile.

Le pale originali in legno avevano la ricopertura in termoretraibile che si allentava
di continuo e dava problemi quando il rotore girava molto forte.
Quindi le ho scoperte e poi ricoperte in sottovuoto con fibra di vetro da 80 grammi per
metro quadro e resina epossidica. Dopo questa operazione e' necessario bilanciarle di
nuovo. Non sono ancora state provate in volo in quanto sto volando con pale SAB in
carbonio.
Per il sottovuoto ho usato la macchinetta autocostruita che si vede in foto. Viene usata
normalmente per incollare i rivestimenti delle ali degli aerei.
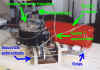
Per ora direi che e' tutto.
Sperando possa aiutare a risolvere problemi a qualcuno.
