All
Bassoon Cane Reed Tips
There
are many different opinions about reed design and styles. In
fact, if you count the number of Bassoonist in the world, including
myself, this will approximate the number of opinions available. What
I
will do is try to share ideas that I developed/learned from others and
pass them on to you. You decide if they work for you. If you have
constructive comments that you wish to share with me, send email to
Tony.
How to improve the tip opening:
There are publications available today that talk about beveling the tube
of the reed to improve sealing the tube end of the reed. But, the publication may
caution you if the throat dimensions are small this may lead to an even
narrower throat. But, what I have learned that there is a major benefit
to beveling. If done correctly, the bevel will cause the tip to have
more spring(i.e. bounce) to the opening. We all know squeezing the 2nd wire from the
top/bottom has the effect of opening the tip. This effect is identical
for the 3rd wire as well. By beveling the tube correctly, the third
wire, when tighten, will produce this opening effect. What I do that I
think is unique is to start the bevel at the second wire back to the butt
end. With the lightest bevel closest to the second wire and gradually getting
wider towards the butt end. This will avoid the problem of narrowing the throat since
technically the throat is between the 1st and 2nd wire.
Improving the tip opening even more:
There is another technique that works even better but is much harder to
do and will require special machinery. You gouge your cane to a common
thickness of .050", starting at the second wire you gradually vary the
gouge, linearly, until you reach .030" at the butt. You'll get more
spring in the tip plus, you'll reduce the cracking, if not eliminate,
when forming the tube.
Wiring/Wrapping:
When I form my blanks, I use 22-gauge wire for the 1st wire and 23 gauge
wire for the 2nd and 3rd wires. If I could, I would use 23-gauge for
the 1st but it not strong enough to help maintain the tip opening. So,
why do I use a smaller gauge wire? The least amount of restraint that I
can apply to the cane the more it will vibrate. There is less surface
area that touches the cane using a smaller wire.
When wrapping the reed there are many methods (string, shrink tubing,
hot glue, melted toothbrushes, bare, .etc). I prefer the string. I use
a cotton-based string. It tends to expand a little more than the
popular polyester based strings. I wrap the reed using a Turk's head
style wrapping. To help key the wrapping intact, I use an acrylic based
lacquer[5]. Dries hard like nail polish, but since it's water based it
doesn't have that toxic smell like nail polish, glue, or regular lacquer. So, when
completed, I feel I have a good wrapping with minimal damping to allow
the reed to vibrate a free as possible. In conjunction with using
different gauge wiring, I find that the combination of these subtle
changes do make an improvement in the final results.
Another form of wrapping, that seems to work very well
and is good for Bassoonist in dry climates is using Plastic Dip. It's used to put rubber
handles on shop tools. You can get it at the hardware store in either black or red.
You paint the reed with this thick goop or plug the butt-end with a little cork,
sold in hardware stores, and dip the reed in the goop. Let it dry overnight. It really shrinks
and sticks to the reed and since it's rubber, it flexes. I doubt this will ever come off if the reed
gets really dry and the tube shrinks[6].
Wires:
Before you make any scrape adjustments to the reed, make sure your wires
are adjusted correctly and have the proper tension. For example if you
find the reed has too much buzz to the tone quality and the pitch is
sharp, it maybe the first wire is too loose. Or perhaps you find the
tone too stuffy, it may mean the opening at the second wire is too
round. Many times a typically geometry for the 1st and 2nd wires works
for an individual player, but depending on the cane, you may have to
vary it. Once you scrape, it's too late and you may ruin a reed.
Always check the wire first!
Blade slippage:
If you find that your blades are slipping here are a few
common causes.
1. Do your blades slip shortly after you cut the tip? If so,
you've twisted the mandrel too much in one direction when forming the
reed. When I form reeds, I soak the cane for 25-35 minutes in hot water
[1]. I score, install the first wire, and wrap the reed in a large
rubber band. I use a heated mandrel. With forming pliers holding the
blank, I slightly open the back end of the reed and insert the mandrel.
I use no twisting action at all. If you twist, you need to make sure
for everyone clockwise motion to need a counter-clockwise motion that is
equal. Basically, you need to cancel the twisting force.
2. Do your blades tend to slip after some use? Is the reed butt
reamed properly? If not you are probably using too much force twisting it on the
bocal. You can detect this if you notice the blades are always slipping
to one side. A properly fitted reed will almost just slide on with a
little twist. Not too much force!
3. Did you ream the reed after you cut the tip and when it was wet?
Wait till the blank is dry. The reamer will cut easier and you'll
require less force to do it.
Forked E-flat:
I find that the forked E-flat, without the right hand, is a good
indicator of a reed's potential. The goal is to get a minimal
difference is pitch and tone quality with(xox oxo RT B-flat) and without
the right hand(xox ooo). Thinning the wings is usually where the
adjustment is made. Avoid the rails. The arrows indicate the direction
of your knife.
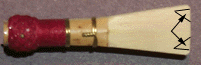
A/B flat Improved Attacks:
If you find that the A/Bb are speaking clearly, you made need to cut the
windows in the heart. I'm not talking about the notes cracking during a
slur (up to or down to) or fast/loud staccato passages. These require
judicious use of the speaker keys (flick keys). Look at the diagram
below and add the windows to either side of the spine towards the tip.
Just do a little bit at a time. Remember you can't put the cane back.
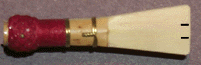
D Above the Staff:
Typically this note is flat, but if you find it flatter than normal or
stuffy, you may need to thin the corner rectangles of the reed(1 mm x 3 mm). See the
diagram below.
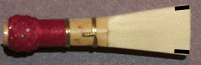
Tools:
The best pair of wire cutters I've used is a toenail clipper. It's
cheap, it last a long time and it cuts very well [2].
To score cane I use two devices, both hand made. As a holding board for
the cane, I took a 1 in. dowel, cut it in half. Glue and/or screw the
dowel, flat side down onto a piece of 1x3 oak board [3]. Added some
rubber feet and it's done.
Making a scoring tool is easy and saves a lot of time [4]. Using 5
blades screwed together with spacers in-between to separate the blades.
I used fiber washers that you can get from the hardware store. The
blades are used for utility knifes and they must have a hole in the
center for the screw to go through. So, it's like making a sandwich.
You alternate a blade and a washer. Use a nut a bolt to hold it
together and wrap on end with duct tape so you don't cut your hands.
Careful, the blades are sharp. You add or remove blades to change the
number of scores.
So, you place your cane on the hold board and use the scoring tool to
score each side of the reed, simple and effective.
The most important tip of all:
Allow the cane to settle between steps. When we gouge cane here at All Bassoon Cane,
it has typically aged before we use it. After you form the reed, let it sit for a minimum of
one week to accept its new shape. Longer is better. Make a bunch and let them age
for a couple of months or so. When you are ready to finish the blank, do the first level
and let it dry for a few days. Finally, soak the reed and make some final adjustments
over a period of a couple of sessions until it's the way you like it. I have learned, by taking
this approach I produce better reeds.
[1] Cane was dry and it was gouged, shaped, and profiled.
[2] Credit Gerald Corey
[3] Credit Arthur Grossman
[4] Credit Scott Vidger
[5] Credit Bill Roscoe
[6] Credit John Lindberg
|